Implantation mondiale
Amérique du Nord
> Park City (Utah)
> Montréal (Canada)
Europe
> France
> Italie
> Allemagne
> Autriche
> Suisse
> Norvège-Suède
Asie
> Japon
> Chine
42 pays via nos
distributeurs
> Espagne
> Pologne
> Russie
> Finlande
> Corée
> …
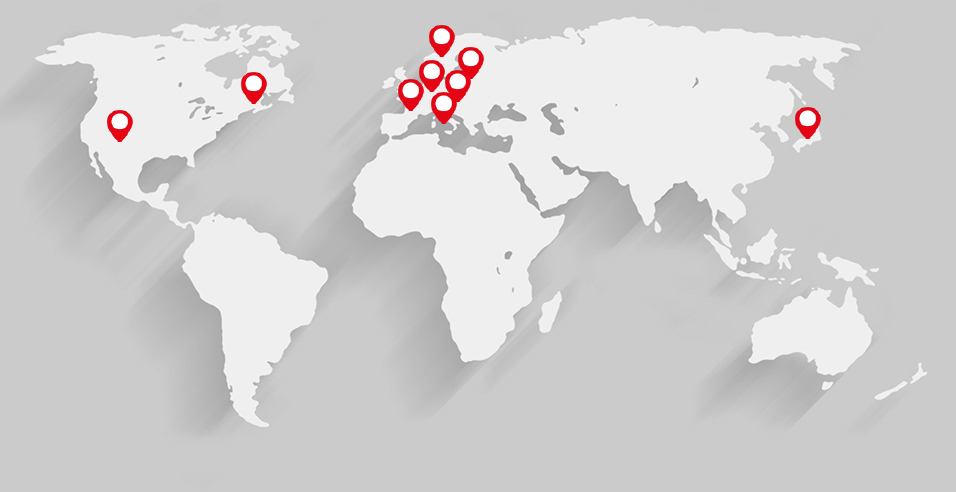
Les sites industriels
Le Groupe possède 4 usines en Europe, dont deux en France :
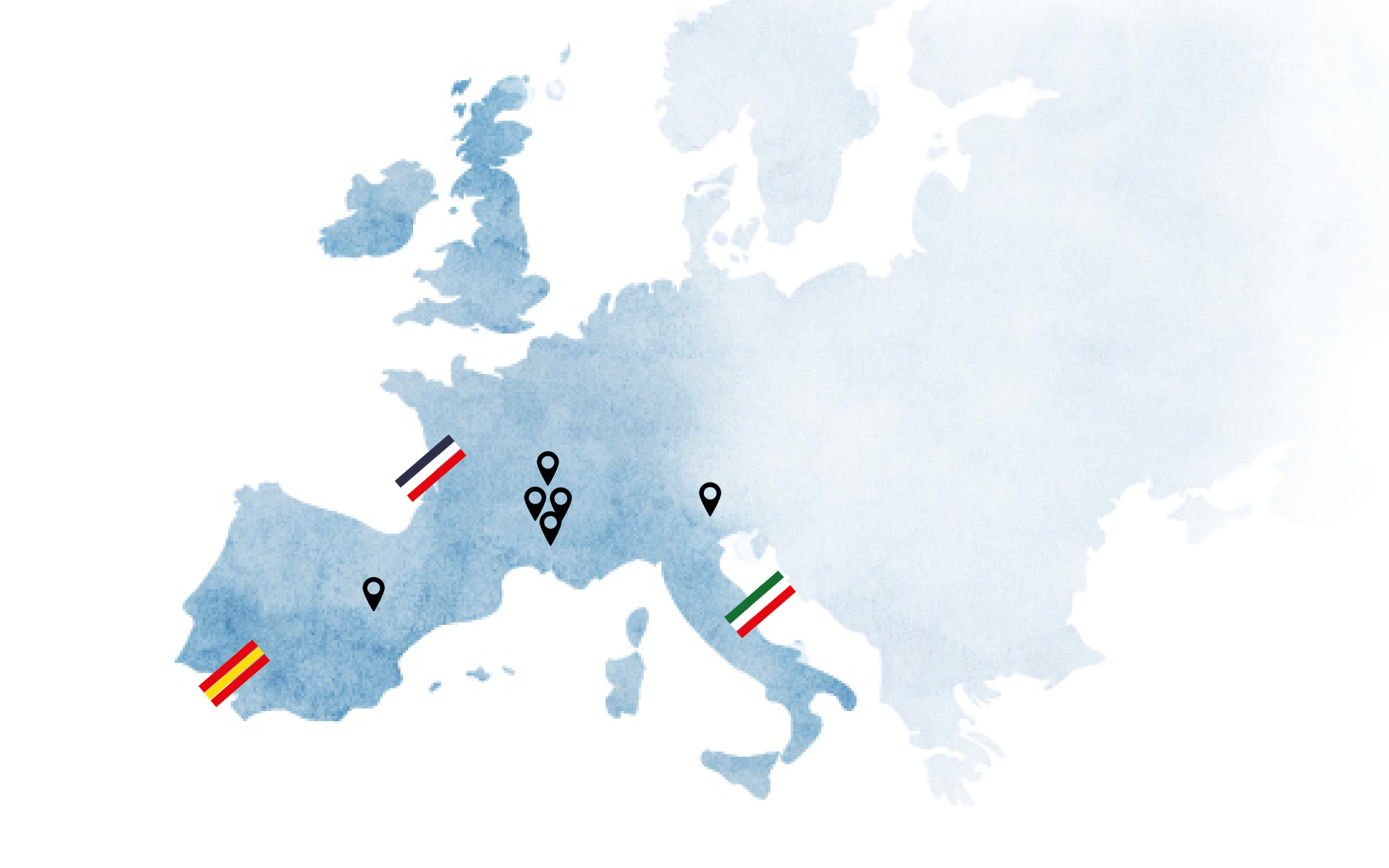
> Sallanches : production, au pied du Mont-Blanc, de skis alpins haut de gamme en petite et moyenne séries pour Rossignol et Dynastar et de skis pour les gammes Junior.
> Nevers : fixations sous la marque Look, N°2 mondial.
> Artés (Espagne) : site dédié à la production des skis alpins en noyau bois, de technologie traditionnelle pour les marques Rossignol et Dynastar et les skis de fond haut de gamme.
> Montebelluna (Italie) : chaussures alpines haut de gamme sous les marques Rossignol et Lange, patins à glace haut de gamme Risport. Centre d’expertise en conception/design pour les chaussures (incluant le Footwear Rossignol).
> Entrepôt logistique central basé à Saint-Etienne-de-Saint-Geoirs/ Isère.
> Hub global Apparel & D2C en Italie à Milan.
ESPAGNE – SITE D’ARTÉS – SKIS
L’usine d’Artés, qui a fêté en 2022 ses 50 ans d’existence, est dédiée à la production des skis alpins en noyau bois, pour les marques Rossignol et Dynastar et des skis de fond haut de gamme Rossignol. Le site espagnol est aujourd’hui responsable de 78% de la production mondiale de skis alpins du Groupe. Le site assure aussi la production des skis Nordic.
L’usine de skis d’Artés est un modèle de l’engagement de Rossignol pour une production plus respectueuse de l’environnement. Elle fonctionne grâce à 100% d’électricité renouvelable depuis 2018 et produit une partie de son électricité grâce à l’installation de panneaux photovoltaïques installés en 2023.
L’ensemble du processus de production a été révisé et optimisé pour limiter l’impact environnemental.
4 000 panneaux photovoltaïques ont été installés avec l’objectif de produire 20% des besoins d’énergie électrique annuels.
Le site d’Artés bénéficie par ailleurs des certifications nécessaires pour l’utilisation de noyau bois PEFC.
Le label PEFC garantit au consommateur que le produit qu’il achète est issu de sources responsables et qu’à travers son acte d’achat, il participe à la gestion durable des forêts. Gérer durablement une forêt, c’est prendre en compte ses dimensions environnementales, sociétales et économiques. Une mission qu’accomplit chaque jour le label PEFC en tant que gardien de l’équilibre forestier. Ainsi, ce label assure un suivi des bois certifiés depuis la forêt, et tout au long de la chaine de transformation et de commercialisation, pour aboutir en fin de chaine à la certification du produit fini.
ITALIE – SITE DE MONTEBELLUNA – CHAUSSURES
Le site de Montebelluna est le centre d’expertise dédié aux chaussures de ski et Footwear. Le site est en charge de la conception et de la fabrication des chaussures de ski alpin des marques Rossignol et Lange, ainsi que de la conception des patins à glace haut de gamme Risport.
Les emballages ont aussi fait l’objet d’une vigilance particulière puisque le Groupe Rossignol a d’une part veillé à réduire leur utilisation au maximum et d’autre part s’est fourni en cartons labellisés FSC® pour emballer ses gammes de chaussures.
Le site fonctionne à 45% d’électricité d’origine renouvelable.
Le processus de production des coques par injection génère des déchets plastique (rebuts et carottes d’injection). Afin de les réduire les déchets, ils sont rebroyés sur place et réintégrés dans la fabrication dans de nouvelles coque.
Plus de 100 personnes employées, dont 30% en R&D et design.